HEALTH AND SAFETY
The Company works closely with our business partners to ensure that Workplace, Safety and Health (WSH) practices are strictly adhered to and continuously improved. In line with our corporate Environmental, Health and Safety (EHS) Policy established in the early 2000s, interim targets have been established and reviewed quarterly to keep track of our EHS performance, ensuring high and consistent standards. We continue to be recognised as a long-serving bizSAFE Mentor.1 In 2023, we concluded our recertification audit and maintained the integrated ISO 14001 and ISO 45001 environmental, health and safety management system certification, reaffirming our commitment to upholding the highest levels of occupational health and safety through the applications of industry-leading practices.
The Company’s leadership places strong emphasis on EHS. Our Group CEO, Board of Directors and senior management are committed to adhere to the Code of Practice for Chief Executives’ and Board of Directors’ WSH Duties (ACOP)2, and guide the Company in establishing and maintaining highly effective EHS standards. Through the Company’s integrated EHS Management System, our leaders drive strategic initiatives to safeguard the safety and health of all employees and workers. This includes regular engagements with employees and workers as well as attending internal and external trainings to keep abreast of the latest EHS developments and industrial best practices. In 2023, the Company conducted 19 ExCo and senior management engagement sessions across 16 managed buildings and construction sites, engaging more than 250 employees and workers.
Our Approach to EHS Risk Management
The Company prioritises the health and safety of our employees and workers at our managed buildings and construction sites. While not direct hires of the company, contracted site and building workers are protected under the Company’s stringent health and safety management policies and procedures.
- The BSC, composed of Independent Directors and the Group CEO, holds accountability for EHS and sets the Company’s EHS Management System (EHSMS)’s intention and direction. The BSC is supported by an Executive Committee which performs the operationalisation and implementation of the measures listed within the ACOP and ensures compliance with ISO 14001 and ISO 45001 standards and legal regulations, as well as a Steering Committee which ensures adequate resourcing across business units and operational processes are consistent with the Company’s objectives and policy. The Group’s employees are represented in the EHS Working Committee through their department representatives. This provides an open channel for employees to raise EHS issues and concerns to the EHS department. The committee convenes at least once annually to discuss and review the Group’s approach to health and safety management, with regular communication and updates
- Our EHS Working Committee members undergo risk management training to lead risk assessments for their respective operations and attend refresher sessions periodically to keep abreast of new industry standards and regulations. In 2023, the EHS Working Committee broadened its representation with the inclusion of additional business units and our subsidiaries to ensure more comprehensive coverage and equitable participation
- Trained internal auditors support the EHS department to assess the effectiveness of our EHSMS through annual internal audits carried out with predetermined scope and guidelines
- The Company reviews our EHSMS at least once annually during our Management Review meeting, chaired by the Group CEO and attended by the Company’s Management. Employees are encouraged to actively engage in EHS practices and raise any concerns and issues related to health and safety to the EHS Committee. This can also be done through the CDL Whistleblowing Channel, a secure and anonymous platform
Hazard Identification, Risk Assessment and Risk Control |
||
|
||
Responding to Incidents |
||
|
||
Internal and External Audit |
||
|
||
Training |
||
|
||
Health and Well-Being |
||
|
CDL Group’s Safety Performance
Occupational safety and health is at the forefront of all our business processes. Since 2003, we have maintained our OHSAS 18001 certification that demonstrates our commitment to a holistic occupational health and safety management system. In March 2020, OHSAS 18001 was migrated to the latest ISO 45001 standard. It provides robust guidance for our integrated EHSMS that covers 100% of our key operations in Singapore.
In 2023, we extended the monitoring of our EHS performance to the Group level, including subsidiaries and M&C Hotels operations in Singapore. There were no fatalities, high-consequence injuries3, dangerous occurrences or cases of occupational disease involving our employees at the Company’s corporate office. There was one reportable injury (trip and fall) that involved CDL Corporate Office staff. At the Group level, there were 102 work-related injuries involving the Group’s employees, mostly from the operations team. Root causes were identified and corrective actions were taken.
The table is scrollable to right
CDL Group’s employees’ safety performance | ||||||||
2023 | ||||||||
Corporate Office | Le Grove | City Serviced Office | City Nexus | Tower Club | CBM Pte Ltd | M&C Singapore | Group Overall | |
Number of reportable work-related injuries4 | 1 | 1 | 0 | 0 | 0 | 58 | 42 | 102 |
Number of fatalities | 0 | 0 | 0 | 0 | 0 | 0 | 0 | 0 |
Lost-Time Injury Frequency Rate5 (number of lost time injuries per 200,000 manhours worked) |
0.3 | 2.9 | 0 | 0 | 0 | 2.1 | 3.1 | 2.2 |
Lost Workday Rate6 (number of lost man-days per 200,000 manhours worked) |
4.1 | 14.4 | 0 | 0 | 0 | 19.5 | 22.6 | 18.7 |
Absentee Rate7 (% of total workdays scheduled) |
2.5 | 2.8 | 1.5 | 1.2 | 3.3 | 2.6 | 1.8 | 2.3 |
Absentee Rate (as % of employees)8,9
FY2020 | FY2021 | FY2022 | FY2023 | |
No of employees | 415 | 408 | 406 | 3,543* |
Absentee rate (% of total workdays scheduled) | 1.5% | 1.3% | 2.3% | 2.3% |
* In 2023, we extended the monitoring of our EHS performance to the Group level, including subsidiaries (Le Grove, City Serviced Offices, City Nexus, Tower Club, CBM Pte Ltd) and M&C Hotels operations in Singapore.
1 | bizSAFE Mentors are organisations that have demonstrated excellent WSH performance and leadership. As a role model, a bizSAFE Mentor shares good practices and nurtures bizSAFE Enterprises in their WSH, guiding them as they progress in the programme |
2 | Code of Practice on Chief Executives’ and Board of Directors’ WSH Duties (tal.sg) |
3 | A high-consequence injury is a work-related injury that results in a fatality or in an injury from which the worker cannot, does not, or is not expected to recover fully to pre-injury health status within six months |
4 | Reportable incidents refers to all work related deaths, illnesses and injuries which result in a loss of consciousness, restriction of work or motion, permanent transfer to another job within the company, or that require some type of medical treatment or first-aid |
5 | Lost-time injuries frequency rate (LTIFR) is any work-related injury that results in the company employee or third-party contractor employee not being able to return to work the next scheduled work day/shift or which result in death or permanent disability |
6 | The Lost Workday Rate is a standardized metric that provides a measure of the total number of working days lost within a workplace due to occupational injury or illness |
7 | Absentee rate was based on medical leave taken regardless of whether it was a work-related illness or not |
8 | Absentee rate (AR): It is based on the total number of days lost due to absenteeism of any kind, not only as a result of work-related injury or disease. This includes individual sick days due to minor illnesses (e.g. the common cold, fevers, and influenza) as well as personal days taken for undisclosed reasons. It does not include scheduled or permitted absenteeism such as holidays, study time, maternity or paternity leave, etc. |
9 | Absentee rate calculation: [Number of absentee days in the accounting period / Total days scheduled to be worked in the accounting period] x 100 |
CDL Group’s contractor safety performance
CDL Group’s contractor safety performance | |||
2023 | |||
Managed Buildings | Construction Sites | Overall | |
Number of reportable work-related injuries6 | 7 | 1 | 8 |
Number of fatalities | 0 | 1 | 1 |
Lost-Time Injury Frequency Rate7 (number of lost man-days per 200,000 manhours worked) |
2.2 | 0.03 | 0.2 |
Lost Workday Rate8 (number of lost time injuries per 200,000 manhours worked) |
32.2 | 0 | 2.6 |
Total WSH at Managed Buildings
Effective facilities management and maintenance are vital in delivering prompt and reliable services to our tenants, customers and building users. This impacts operational efficiency of our managed assets and our bottom line. Thus, we place great emphasis on guiding our facility managers and contractors to uphold safe, healthy and productive work environments for workers in our managed buildings. In addition, we actively engage our tenants to seek their feedback on any unsafe conditions and provide prompt resolutions.
Contracted workers are engaged through monthly meetings to develop solutions that mitigate WSH risks and to reiterate the importance of health and safety issues. The majority of our contracted workers, who are not directly employed by the Company but work at our premises, are from our wholly-owned subsidiary, CBM Pte Ltd. In 2023, an average of 254 CBM workers per quarter worked at the Company’s managed buildings.
Robust risk assessments at our managed buildings are led by our trained personnel in operational risk management. For every facility management assignment in our properties, suppliers are required to perform risk assessments to mitigate safety risks, such as falling from heights that could result in bodily injury or fatality. To manage this, it is mandatory for all supervisors and workers to attend a ‘Working at Height’ course.
In 2023, there were no fatalities, high-consequence injury, dangerous occurrences and occupational disease involving the workers of our key contractors8 at the Company’s managed buildings. There were seven reportable injuries (e.g., trip and fall, sprains), which were classified to be minor. These were sustained by our contractors’ workers and resulted in a loss of 104 man-days. Root causes of these injuries were identified and corrected immediately to prevent a recurrence. Lessons from all incidents were actively shared with the respective managers, EHS working committees and contractors. We continue to work closely with the contractors to strengthen the risk control measures of their daily operational activities.
Total WSH at Construction Sites
The Company prioritises our workers’ health and safety through the enforcement of policies and practices. Measures to manage and minimise high-risk activities include:
- Robust risk controls, such as fall prevention plans and regular personnel protective equipment inspections
- Frequent briefings on dengue, fatigue, heat stress, hearing conservation and respiratory protection
- Regular on-site inspections for health and safety risks
For close to two decades, it has been mandatory for our builders to possess an accredited health and safety management system, such as ISO 14001, ISO 45001 or minimally a bizSAFE Level 3 certification, as a component of the tender assessment process. We also actively engage our business partners on health and safety matters through risk reviews, covering the whole life cycle starting from pre-construction to Temporary Occupation Permit (TOP) attainment. In 2023, one of our main contractors achieved the Safety and Health Award Recognition for Projects (SHARP) awards for Amber Park. This award recognises large-scale projects or worksites that have good safety and health performance and workplace safety and health management systems.
A customised EHS risk register is used for each construction site to identify and mitigate EHS issues from the design stage. The type of construction materials and methods to be adopted are actively reviewed to mitigate any EHS risk.
Each construction site has a dedicated workplace EHS committee, representing all workers on-site, including members from the main contractor’s management, construction workers and sub-contractors. Our project managers regularly track workplace EHS issues at meetings conducted on-site with our main contractors and workers’ representatives. This allows close oversight of on-site issues, ranging from technical challenges to workers’ welfare. These meetings serve as a platform for site coordinators to report unsafe work conditions and propose risk mitigation plans. Some of our sites further incentivise workers to identify and report risk, to raise overall safety awareness.
For every construction, a monthly joint safety inspection is carried out in the presence of the main contractor, sub-contractors and site staff representing the Company and our consultants. The inspection highlights safety infringements and promotes better work conditions. Since 2001, on top of regulatory mandated audits, we also monitor the performance of the main contractor’s EHS management through our CDL 5-Star EHS Assessment.
In 2023, an average of 3,131 construction workers worked at our developments. Across our 11 active construction/ demolition sites throughout the 12-month period in 2023, an average of 29 workers were involved in every 1,000 m2 of built area.
In 2023, there was one fatality at the Newport Plaza construction site during the demolition phase, despite the Company’s best efforts to assure site safety. We worked closely with our contractors and cooperated with the authorities on the investigation. As the incident occurred during the demolition phase, prompt remedial action was taken to address any gaps in operations to ensure good health and safety practices on-site. There were no high-consequence injury, major injury, minor injury, dangerous occurrence and occupational disease at the Company’s construction sites. There was also no other reportable injury6 that occurred within the Company’s construction sites.
6 | Reportable incidents refers to all work related deaths, illnesses, and injuries which result in a loss of consciousness, restriction of work or motion, permanent transfer to another job within the company, or that require some type of medical treatment or first-aid |
7 | Key contractors in our managed buildings provide cleaning, security services and mechanical and engineering support. Working hours disclosed covers the Company’s employees and workers of key contractors only |
8 | The Lost Workday Rate is a standardized metric that provides a measure of the total number of working days lost within a workplace due to occupational injury or illness |
CDL 5-Star Assessment, Awards, Quarterly Seminars and EHS Sports Challenge
The CDL 5-Star EHS Assessment was established in 2001 as an independent audit tool to assess, measure and improve main contractors’ EHS management and performance. It has been instrumental in influencing the Company’s main contractors’ and consultants’ EHS performance. It ensures a comprehensive, audited, and appraised approach. All the Company’s main contractors are required to undergo monthly EHS inspections and audits conducted by an independent audit firm recognised by MOM, and are appraised in areas such as energy, water, waste management, safety, noise and public health management. Results are then presented to the management and site supervisors of the contractors and consultants during the quarterly CDL 5-Star EHS Seminars, which facilitate sharing of best practices to encourage peer learning and improvements.
Launched in 2005, the CDL 5-star EHS Awards recognises exemplary builders and workers who have excelled in the CDL 5-Star EHS Assessment during the reporting year. The Company’s construction sites scored the highest rating of five stars, determined by the average performance across the year.
EHS Sports Challenge
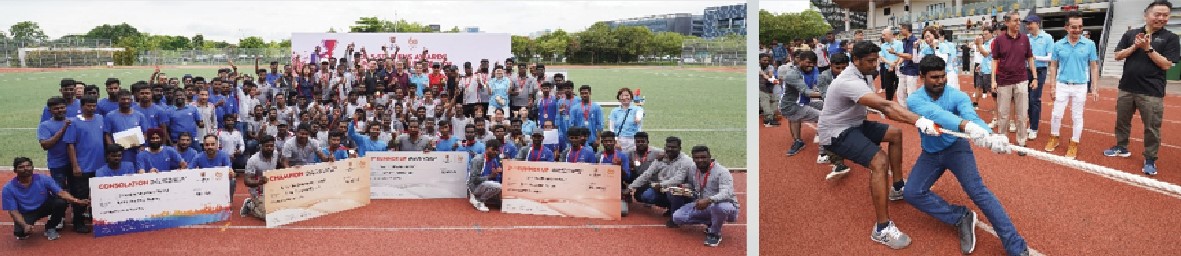
The EHS Sports Challenge is an annual staple event organised to promote workplace safety and foster workers’ camaraderie through sports and engagement activities. In November 2023, approximately 160 migrant workers with their sub-contractors and consultants gathered at the Singapore University of Technology and Design’s stadium for a day of competitive tele-matches, interactive game stations and educational exchanges covering a spectrum of WSH practices. The 2023 sports event was graced by Singapore’s Minister of State for National Development and Home Affairs, Associate Professor Dr Muhammad Faishal Ibrahim, as well as senior representatives from the WSH Council.