ENSURING SUPPLY CHAIN RESILIENCE AND SUSTAINABLE SOURCING
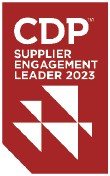
With the Company’s pledge to the WorldGBC Net Zero Carbon Buildings Commitment and responsibility towards green and responsible procurement, consistent engagement with our supply chain is pivotal for a net-zero whole life carbon built environment.
Testament to our robust efforts in working with our supplier network to address climate change, we were the only real estate company in Southeast Asia and only Singapore company to be awarded the 2023 CDP Supplier Engagement Leader for the fourth consecutive year. This recognition places the Company amongst the top 2% of companies assessed by CDP for supplier engagement on climate change.
For many businesses worldwide, Scope 3 emissions can account for more than 70% of their carbon footprint.1 Measuring and managing these emissions motivates a company to choose more sustainable suppliers, improve the energy efficiency of its products, and rethink its sourcing and distribution network — measures that can significantly reduce the overall climate impact.
Critical Supplier Identification
The Company engages various types of suppliers across our value chain and operations. We identify and work closely together with our Tier 1 supply chain partners to prevent disruption to delivering quality products and services.
Procurement of Sustainable Materials
For more than a decade, the Company has implemented sustainable procurement guidelines that set clear specifications for responsible sourcing along our supply chain. This includes the Responsible Procurement Guidelines3 since 2008, and the Green Procurement Guidelines for property developments since 2009. In line with our corporate EHS Policy introduced in 2003, these guidelines encourage the use of eco-friendly and recycled materials that have been certified by approved local certification bodies, such as Singapore Green Building Council (SGBC) and Singapore Environment Council (SEC).
In 2021, we updated our 3S Green Building Framework to align with the latest BCA Green Mark 2021, an internationally recognised green building certification scheme, to stay focused on advancing our commitment to sustainability. The revised framework also included net-zero targets such as embodied carbon management to promote sustainable building practices.
Our green procurement guidelines also indicate our preference for ISO 14001, ISO 45001, and bizSAFE Level 3 certified suppliers/vendors. In key operations like property development and asset management, major suppliers and builders must meet the EHS pre-qualification criteria. They are required to sign a supplier code of conduct, which provides comprehensive guiding principles for our vendors and suppliers to comply with the Company’s expectations, including environment, health, safety, and ethical employment.
We have established a target to ensure 100% of our appointed suppliers are certified by recognised EHS standards by 2030. In 2023, 100%4 of our main contractors and key consultants for property development had recognised EHS certifications. In our asset management division, 100%4 of suppliers5 appointed were certified by recognised EHS standards.
Supply Chain Engagement
The Company assesses risks in our supply chain through regular engagement with our upstream suppliers and operational policy alignment with latest regulatory developments. We conducted a detailed supply chain segmentation study on our top 100 suppliers and top five raw materials used in 2019, which helped to strengthen the Company’s understanding of how emerging trends such as automation and climate change present risks and opportunities, including forced labour and migrant risks to our supply chain strategy. With no significant change to our supply chain in 2023, the study continues to guide our approach in addressing labour risks within the region.
To ensure a healthy and safe working environment, representatives of the Company’s ExCo, senior management and key executives from business units engaged with workers regularly at our construction sites, managed buildings, and corporate office on WSH matters. The Company also guided our main contractors on the use of carbon calculation tools and accounting methods to evaluate the embodied carbon of respective projects completed in 2023. The aggregated data was eventually externally audited to ISO 14064 Greenhouse gas requirements. This process enhanced the contractors’ awareness and proficiency in carbon accounting, a skillset of growing importance.
1 | Greenhouse Gas Protocol, 4 April 2016 |
2 | The Company’s Tier 1 Suppliers are classified as critical, high volume and/or non-substitutable |
3 | Renamed from Green Procurement Guidelines in 2020 |
4 | Of the new suppliers appointed in 2023 by AM and PD, 100% were certified by recognised health and safety standards (e.g. ISO45001, OHSAS18001, and minimum bizSAFE Level 3 Certification), and 52% were certified by recognised environmental standards (e.g. ISO14001) |
5 | For asset management, this target applies to vendors engaged for proprietary equipment service and maintenance, facility management, security and cleaning service in the reporting year |